The Ultimate Guide to Metal Forging Suppliers: What Every Industry Needs to Know!
Discover essential insights on choosing the right metal forging supplier for quality, efficiency, and industry needs.

The process of manufacturing of high-strength and durable components utilized in numerous industries such as automotive, aerospace, construction, power generation, and many more, lies in the most critical step known as metal forging. All those industries, which have heavy dependency on metal forging, now face a critical requirement of selecting a suitable forging supplier to produce parts of quality to meet all specified requirements. Whether it's custom components, bulk supplies, or innovative forging technologies, the idea of your business can never materialize unless you know what to look for in a metal forging supplier. This comprehensive guide will let you in on everything there is to know about metal forging suppliers and the best way to find the right supplier for your business.
What is Metal Forging?
Metal forging is a manufacturing process where heat-treating is applied to the metal, and under pressure, it is moulded into parts that would have exceptionally great strength and durability. Unlike most other methods in casting or machining, the nature of this process results in the components leaving with superior mechanical properties such as increased toughness, greater resistance to fatigue, and structural integrity. Some of the other types include open die, in which the metals are moulded by placing them between two dies, and there is close die forging, in which the metal has to be compressed into a certain die cavity. The other process is upsetting, in which part sections are created with more substantial sides. Ring rolling is one common method for creating rings of uniform cross-section. The decision of each forge process is mostly determined based on the component design criteria and strength with regard to the respective strength necessities of that component; always a right process is chosen for optimized performance.
Why the Best Metal Forging Company
The ideal metal forging supplier isn't one who quotes the minimum price but some who can show that they are reliable concerning delivering quality high-standard, Industry Compliant-Compliant- components every time. The wrong choice might end up causing mistakes, delayed orders, and lower quality products, which would jeopardize your operation. Quality assurance is the main reason for the right supplier; a credible supplier will always be ISO 9001 certified to assure that high quality control will always be guaranteed on every part delivered. Another significant point is efficiency, where timely delivery from the reliable supplier will not lead to a bottleneck in the production of products. In addition, most companies need forging products for a given application. Therefore, an efficient supplier must be of a capacity wherein they must have the capability to work in tandem to create the exact component needed based on your specifications.
What to Expect from Your Metal Forging Supplier
To be able to select a good metal forging supplier, the following should be your consideration factors:
1. Experience and Expertise
Find a supplier with years of experience in the metal forging industry. Years of experience about any organization will translate directly to experience in very complicated designs and working with different varieties of materials to be able to cope up with great requirements of performances. Further, detailed specific experience can also be desirable with industries in like aerospace and automobile, more about your very requirement.
2. Certifications and Compliances
This helps evaluate the ability of a metal forging supplier to meet the conditions posed by industry standards and sustain the level of quality. Major certifications to be sought include ISO 9001, which verifies that the supplier is following the proper quality management systems, AS9100 for aerospace parts with specific requirements set by the aviation industry, and IATF 16949 for automotive parts to ensure that the supplier has the quality standard for the automobile industry. These accreditations ensure that a supplier follows some standard and necessary legislations. Ensure that your supplier gets these accreditations in a bid to prevent defects, safety of the products, and to ensure that the forged parts are developed according to exact specifications.
3. Advanced Technology and Equipment
Advanced machinery is mandatory in the forging process to ensure it is accurate and of quality. Ensure the supplier employs technologies like CNC machining, automated forging systems, and 3D scanning to ensure quality assurance. Suppliers who employ advanced technology can guarantee higher accuracy and better turnaround time.
4. Material Expertise
The right supplier should understand deeply materials like carbon steel, alloys, stainless steel, and titanium and the capability to work with high-performance materials for extreme conditions. He or she must be able to suggest the best material for your application.
5. Capacity and Lead Time
Ensure that the supplier can accommodate your required production volume when you order for small batch or high-scale production. Equally important is assessing their lead times and capacity to meet timelines since forging delays can upset the overall production time.
6. Cost Competitiveness
Though not the only concern, it is one of the major ones. Quote many suppliers, compare their offers but make sure that the quotation delivered is related to the quality of parts used and the quality of service that will be met. Not skimping just to cut corners will have poorly made products or a nonfunctional end product.
7. Customer Service and Communication
A good supplier would be able to give good customer service and be responsive to your needs. They will have a good, open, and transparent line of communication from the initial inquiry through to final delivery. Good customer support assurance makes the issues disappear within a short period of time and fulfils all your needs.
Top Industries That Rely on Metal Forging
Metal forging is required in many applications where strength and durability are prime concerns in industries. A number of automobiles need axles, gears, crankshafts, and connecting rods as critical components for the proper performance and longevity of an engine. Forged parts, such as landing gears and engine components with structural parts used in the aerospace industry, endure extreme conditions with the aid of forged material. Oil & gas: In this industry, some drill bits, valve bodies, and pressure vessels are forged to provide enough strength parameters. Construction : structural beams, fasteners and other structural elements of a bridge are made using forged products in order to provide structural stability and longevity. The last one is power generation, where pieces that have been forged, such as the turbine shaft, generator rotor, and coupling allow these machines to bear extraordinary conditions inside power plants. Forging provides the reliability and strength required for the most demanding of industries.
Conclusion
The choice to decide on a metal forging supplier would be of crucial importance and would significantly impact the quality, performance, and cost-effectiveness of your products. Therefore, keeping in mind all the factors including experience, certifications, technological ability, material expertise, and customer service could help to pinpoint a supplier suitable enough who may meet the best needs and thus ensure that highest quality reliable forged components would be provided. It does not matter whether it has to do with automobile, aerospace, construction, or power generation; the difference a right metal forging supplier can make in success makes all the difference.
That is choosing a reliable partner would assist in covering the immediate manufacturing need but would also contribute to its long-term growth and innovation of the business across an industry.
What's Your Reaction?




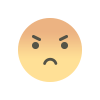

