Water stopper
Water Stopper: An Essential Tool in Construction and Waterproofing
Introduction
Water stoppers are crucial components in construction, designed to prevent water infiltration through joints in concrete structures. They play an indispensable role in maintaining the durability and longevity of buildings, especially in structures exposed to water, such as basements, tunnels, dams, reservoirs, and water treatment plants. A water stopper acts as a barrier within concrete joints to restrict the passage of water and prevent seepage.
This guide provides an in-depth understanding of water stoppers, their types, materials, applications, and importance in construction and waterproofing.
What is a Water Stopper?
A water stopper, also known as a water bar, is a flexible strip or material embedded in construction joints, expansion joints, or other vulnerable areas of concrete structures to block water ingress. It is typically made of materials like PVC, rubber, or metal, which are resistant to water and chemical exposure.
Water stoppers are integral to waterproofing systems, as they seal potential leakage points and ensure structural integrity. They are particularly essential in environments where water pressure is high or where long-term water exposure is expected.
Types of Water Stoppers
1. PVC Water Stoppers
PVC (polyvinyl chloride) water stoppers are the most commonly used type due to their durability, flexibility, and affordability. They are resistant to chemicals and corrosion, making them suitable for a wide range of applications. PVC water stoppers come in various profiles, including dumbbell, ribbed, and center bulb shapes, catering to different joint types.
2. Rubber Water Stoppers
Rubber water stoppers are highly elastic and durable, making them ideal for structures subject to movement or vibration. They provide excellent sealing properties and can withstand harsh environmental conditions. Rubber water stoppers are commonly used in dams, reservoirs, and tunnels.
3. Metal Water Stoppers
Metal water stoppers, typically made from stainless steel or copper, are used in heavy-duty applications where high water pressure or extreme conditions are expected. They are rigid and provide long-lasting protection against water leakage.
4. Bentonite Water Stoppers
Bentonite water stoppers are made from a mixture of bentonite clay and rubber. They swell upon contact with water, creating a watertight seal. These stoppers are ideal for construction joints and areas with irregular surfaces, as they adapt to the contours of the joint.
5. Hydrophilic Water Stoppers
Hydrophilic water stoppers are designed to expand when exposed to water, filling any gaps or voids in the joint. Made from materials like polyurethane or acrylic, they are effective in preventing water ingress in both static and dynamic structures.
Applications of Water Stoppers
1. Construction Joints
Water stoppers are commonly used in construction joints, where new concrete is poured adjacent to existing concrete. These joints are prone to water leakage, and water stoppers provide a reliable seal to prevent seepage.
2. Expansion Joints
Expansion joints in concrete structures allow for thermal movement, shrinkage, and settlement. Water stoppers are essential in these joints to ensure that the movement does not compromise the structure’s waterproofing.
3. Subterranean Structures
Structures below ground level, such as basements, tunnels, and foundations, are highly susceptible to water infiltration. Water stoppers act as a barrier to protect these structures from water damage.
4. Water Retention Structures
In water treatment plants, reservoirs, and swimming pools, water stoppers play a vital role in maintaining water containment and preventing leakage.
5. Dams and Hydraulic Structures
In hydraulic structures like dams and spillways, water stoppers are used to handle high water pressure and prevent seepage through joints, ensuring structural safety and efficiency.
Advantages of Using Water Stoppers
1. Enhanced Durability
Water stoppers prevent water infiltration, which can cause structural deterioration, corrosion of reinforcement, and cracks in concrete. By sealing joints effectively, they enhance the longevity of the structure.
2. Cost-Effective
Although water stoppers add to the initial construction cost, they save significant expenses in the long run by preventing water-related damages and reducing maintenance requirements.
3. Versatility
With various types and materials available, water stoppers can be customized to suit different construction needs and environmental conditions.
4. Chemical Resistance
Water stoppers made from PVC or rubber are resistant to chemicals, making them suitable for industrial applications where exposure to corrosive substances is common.
5. Easy Installation
Modern water stoppers are designed for easy installation, ensuring that they can be incorporated into the construction process without significant delays or complications.
Installation Process
1. Preparation
Before installing a water stopper, the joint area must be cleaned thoroughly to remove any debris, oil, or contaminants. Proper alignment and positioning are essential to ensure effective sealing.
2. Placement
The water stopper is placed in the joint and held in position using clamps, wires, or adhesives. For continuous protection, overlapping sections of the stopper must be welded or joined securely.
3. Concrete Pouring
Concrete is poured carefully around the water stopper, ensuring that it is embedded completely without air pockets or voids. Vibrators may be used to achieve proper compaction.
4. Inspection
After the concrete has cured, the joint is inspected to ensure that the water stopper is functioning as intended and that there are no visible gaps or defects.
Factors to Consider When Choosing a Water Stopper
1. Material Compatibility
Choose a water stopper material that is compatible with the structure’s environment and expected conditions. For example, use chemically resistant materials for industrial applications.
2. Joint Type
Select the appropriate profile based on the type of joint (construction, expansion, or contraction) and the expected movement.
3. Water Pressure
Consider the level of water pressure the structure will be exposed to. High-pressure applications may require metal or specialized water stoppers.
4. Environmental Conditions
Account for temperature fluctuations, UV exposure, and potential chemical contact when selecting a water stopper.
5. Installation Requirements
Ensure that the chosen water stopper is easy to install and compatible with the construction process.
Challenges in Using Water Stoppers
1. Improper Installation
Incorrect placement or installation can compromise the effectiveness of the water stopper, leading to leaks.
2. Material Degradation
Over time, some materials may degrade due to environmental factors, reducing the stopper’s effectiveness. Regular inspections and maintenance are crucial.
3. Compatibility Issues
Using the wrong type of water stopper for a specific application can result in inadequate sealing and potential failure.
Conclusion
Water stoppers are indispensable in modern construction, providing essential waterproofing for structures exposed to water. By preventing water infiltration through joints, they protect the structural integrity and ensure the longevity of buildings and infrastructure. With a variety of materials, types, and applications available, water stoppers offer versatile solutions for diverse construction needs. Proper selection, installation, and maintenance are key to maximizing their effectiveness, making them a cost-efficient investment in any project.
What's Your Reaction?




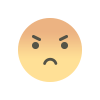

